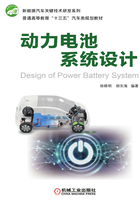
3.1 机械结构设计原理
结构强度校核涉及的知识主要包括理论力学、材料力学、工程力学等,下面对一些基本概念进行简要介绍。
3.1.1 弹性变形体的基本假设
材料力学是以变形固体的宏观力学性质作为基础,并不涉及其微观结构,所以,在进行理论分析时,为了使问题得到简化,可以取弹性变形体作为材料力学中研究对象的理想化模型,但必须做出以下三个基本假设:
1)假设组成结构的固体物质是连续、毫无空隙地充满了固体的体积。
2)假设物体内部各部分的材料性质都是完全相同的。
3)假设在固体的任意一点的各个方向都具有相同的材料性质。
当对构件进行强度、刚度、稳定性等力学方面的研究时,一般在弹性变形范围内将材料看成均匀、连续、各向同性的弹性变形体。实践证明,在此基础上建立起来的分析理论和分析计算结果是能够满足工程设计需要的。
3.1.2 应力应变计算
当直径为d的圆棒,在承受拉力为F的载荷时会引起圆棒变形而伸长,如图3.1所示。

图3.1 圆柱试棒拉伸变形示意图
假设原始长度为l,受力变形之后的长度为l1,则变形量为Δl=l1-l,则应变为

由图3.1可知,除了轴向有变形外,横向也是有变形的,横向产生的应变为

而横向线应变与纵向线应变之比的绝对值为常数,此常数称为泊松比,其表示如下:

而此杆在承受拉力为F时,杆的应力σ可表示如下:

如图3.2所示的受力情况,圆柱试样承受如下所示的载荷,载荷与受力截面平行,此类载荷与前面所述拉伸载荷不同,承受此载荷会使这两个平行面间的任一(平行)横截面产生错动变形,此变形称为剪切变形。

图3.2 圆柱试棒剪切变形示意图
承受剪切载荷所产生的剪切力可表示如下:

承受剪切载荷所产生的角变形量即为剪切应变,可表示如下:

单向应力状态下线弹性阶段的应力应变关系服从虎克定律,即有:

式中,E为材料的弹性模量,将其推广到一般应力状态下各向同性材料下的广义虎克定律,如式(3-8)所示:

以上即为材料在线弹性阶段的材料本构关系。
当冲击引起塑性变形时,文献中有研究运动物体对杆端的纵向冲击问题,如图3.3所示,一个质量为m的大物体沿轴向撞击杆端,物体的初始速度为v,在任一时刻t,应力波传入杆一定的距离,由于连续条件,被撞击的杆端部位移的距离等于杆的端部总的伸长,即有:

应力波的传播速度为,则方程(3-9)变为

故有


图3.3 运动物体对杆端的纵向冲击
上述为线弹性情况,当某点的应力超过材料的屈服强度时,显然式(3-7)~式(3-11)是不适用的,对弹性情况先进行微分,基于微分结果进行扩展是可以得到塑性变形时的本构方程。首先对弹性情况的偏微分方程为

式中,s为位移;ρ为密度;应力波的传递速度。
式(3-12)中的弹性模量E是在初始线弹性范围内的应力应变关系曲线的斜率,当有塑性变形时,可用来替代E,则可以确定应力应变曲线任一位置处的斜率,因此方程(3-12)可以变为:

当材料中的某一点应力超过屈服强度进入塑性状态时,需要通过相关试验获得材料的应力应变关系,如图3.4 所示为单向拉伸应力-应变关系曲线。

图3.4 单向拉伸应力-应变关系曲线
塑性应力与应变关系包括以下几个特点:
1)应力与应变之间是非线性关系。
2)塑性应变是不可逆的,且应力应变关系不是唯一对应。即一个应力可以对应多个应变状态,同时一个应变也可以对应多个应力状态,与加载路径或者加载历史相关。
3)塑性应变时,材料的体积认为是不变的。
3.1.3 材料模型
在复杂应力状态下,材料的应力与应变的本构关系可以归结为函数的关系:

这种函数关系一般与材料特性、结构的变形相关,与应力的状态无关。根据强度理论可知,可选择单向应力状态来建立这种函数关系,单向均匀拉伸或者压缩试验是反映材料力学行为的基本试验,材料开始进入塑性变形的应力称之为屈服应力,在屈服之前,应力与弹性应变呈线性关系,可参考式(3-12)。一般材料在进入塑性状态后,继续变形将会产生强化,卸载后再加载时,材料的屈服应力将增加,这种不断更新的屈服应力称为后继屈服应力,通过试验获得的真实应力-应变曲线一般都是非线性关系。
常用的材料本构模型有理想弹塑性材料模型、幂指数硬化材料模型、刚塑性线性硬化材料模型、弹塑性线性硬化材料模型等。Crush-able材料模型为泡沫类材料或者近似泡沫类材料常用到的材料本构模型,在LS-Dyna里面的材料模型为MAT63号或者MAT163号,除了需要定义密度、初始弹性模量和泊松比外,还需要输入名义应力-体积应变曲线(图3.5),且曲线输入可以基于不同应变率。此模型可以用来模拟裸电池单体受挤压变形时的本构关系。

图3.5 名义应力-体积应变曲线
3.1.4 冲击分析
冲击响应是指结构在承受一定的冲击后,其在载荷作用下所产生的响应,结构所产生的响应大小与系统的固有频率、冲击载荷频率和阻尼相关。冲击响应图谱的横坐标是频率,纵坐标是最大加速度响应值。
在介绍冲击响应谱时,先介绍一下单自由度系统,如图3.6所示,其中F(t)为单自由度系统的基础激励(输入加速度),K为单自由度系统的等效刚度,C为单自由度系统的阻尼系数,M为等效质量。

图3.6 单自由度系统
其数学表达式:

此即为牛顿第二定律。
电池包结构虽然零部件很多,结构复杂,但从本质来讲,还是可以近似为由许多单自由度系统组成的复杂系统,每一个固有频率对应一个单自由度系统。电池包的等效单自由度系统如图3.7所示。在同一冲击载荷条件下,系统的每一个固有频率对应的响应加速度是不一样的,且冲击响应谱具有一定的规律。

图3.7 电池包的等效单自由度系统
根据牛顿定律,对于尖峰脉冲输入,单自由度系统的冲击响应为

当sin(2πfnt)=1时,响应峰值为amaxresp=2πfnΔV,式中ΔV表示加速度变化率,,此计算公式适用于持续时间短的冲击输入。
半正弦脉冲冲击响应谱的特性如图3.8所示。fn为系统结构固有频率,D为冲击载荷持续时间。
1)当fnD<0.3时,系统的冲击响应最大值小于冲击脉冲的峰值加速度,即。因此此段区域的响应可以采用公式(3-16)来预测。
2)当0.3≤fnD<10时,系统的冲击响应大于冲击脉冲的幅值,在此区间内冲击响应具有放大作用,即。
3)当fnD≥10时,。

图3.8 半正弦冲击响应谱
3.1.5 疲劳强度计算
在某点或某些点承受扰动应力,且在足够的循环扰动之后形成裂纹或完全断裂的材料中所发生的局部永久结构变化的发展过程,称为疲劳。提到“疲劳”就会联想到“疲劳寿命”,疲劳寿命的定义是这样的:足够多的扰动载荷作用之后,从高应力或高应变的局部开始形成裂纹,直至到达临界尺寸而发生完全断裂,最后的断裂,标志着疲劳过程的终结,这一发展过程所经历的时间或扰动载荷作用的次数,称为“疲劳寿命”。图3.9所示为关于循环应力与循环次数的介绍。循环的应力幅Sa、平均应力Sm以及应力比R表示如下:


从裂纹扩展的角度,疲劳可以分为高周疲劳和低周疲劳,高周疲劳裂纹扩展规律可利用线弹性断裂力学方法研究:低周疲劳裂纹扩展规律一般采用弹塑性断裂力学方法研究,在现代工业中,80%以上的机械破坏都属于疲劳失效。从疲劳的基本概念可以看出,疲劳具有以下几个特点:
1)导致结构发生疲劳失效的外因是扰动应力,即循环载荷,常见的循环载荷有恒幅值循环、变幅值循环以及随机振动载荷。
2)疲劳往往发生在高应力或者高应变的局部区域。
3)结构在承受足够多的扰动载荷之后,才会慢慢形成裂纹或者完全断裂。

图3.9 循环应力与次数
1.材料的S-N曲线
结构在发生疲劳失效前所经历的应力或者应变循环次数称为循环疲劳寿命,一般用N表示,试样的疲劳寿命取决于材料的疲劳性能和载荷水平,图3.10 所示为结构所承受的三种常见典型载荷:恒幅载荷、变幅载荷以及随机振动载荷。一般地,载荷越低,试件的疲劳寿命越长;反之疲劳寿命越短。这种载荷水平与循环寿命之间的关系能够通过曲线绘制出来,被称为S-N曲线,也称为维勒曲线,图3.11所示为钢材的S-N曲线。循环寿命<103次的疲劳称为低周疲劳,循环寿命在103~106次为高周疲劳,循环寿命超过106次为永久疲劳或极限疲劳。当然,低周疲劳与高周疲劳之间的界限,以及永久疲劳的界限不能由特定循环次数来定义,钢和铝的就不一样。S1000表示疲劳寿命为1000次的疲劳应力幅, Sbe表示永久疲劳应力幅。

图3.10 疲劳载荷类型
2.疲劳累积损伤理论
Miner疲劳损伤累积理论的基本假设:在任何循环应力载荷下结构都将产生疲劳损伤,疲劳损伤的程度与在该应力水平下的工作循环次数有关,与载荷的加载顺序无关,不同应力幅循环下所产生的总损伤等于每个应力水平下的损伤之和。

图3.11 金属材料的应力-寿命曲线
假设在应力σi下材料达到破坏的循环次数为Ni,设D为试件断裂时的临界值,根据Miner理论,应力σi水平下每循环一次对材料的损伤为D/Ni,则经过ni次后,对应的材料累积损伤为niD/Ni,当各种对材料的损伤综合达到临界值D时,材料即发生破坏,理想情况下D为1,即可表示为如下公式:

式(3-20)即为Miner线性累积损伤方程式。线性累积损伤理论显著地简化了疲劳计算,且已经证实其计算结果与实验结果具有很好的一致性。
3.基于极限拉伸强度的S-N曲线估算
S-N曲线是疲劳仿真的基础输入数据,在进行疲劳寿命设计时,常常有些材料没有现成的S-N曲线,如果通过试验获取则需要耗费大量的时间和资源,因此基于前人的大量研究,李永利博士提出了基于有限的信息估算S-N曲线的方法,对于钢制试件,在1、103、106次循环时的强度即可以定义一条S-N曲线,这些疲劳强度值分别对应着S′f、S1000,S′f为修正后的极限抗拉强度,在高周疲劳区域,S-N曲线的斜率b可以用式(3-21)表示:

在双对数坐标下,S=bN,已知点(S1,N1),即可确定S2应力水平下的疲劳损伤循环次数N2:

S-N估算方法
为了获得零件的基准S-N曲线,首先需要确定零件材料的抗拉强度,一旦确定了材料的抗拉强度,在此基础上可以近似得到103次循环、106次循环的疲劳强度,然后基于影响强度的因素考虑对其进行修正,即可估算出有限寿命区域的S-N曲线。
以钢为例,可以根据其硬度对抗拉强度进行估算,对于布氏硬度较低的低碳钢和中强度钢,材料的极限抗拉强度可以被线性近似为:

铸铁的极限抗拉强度可以估算为

极限抗拉强度有了估算的依据后,再来估算S1000和Sbe。103次循环时的疲劳强度取决于加载类型和可靠性水平,一般的:

式中,CR为在规定可靠度下的修正系数;K′f为1000 次循环时的疲劳强度折减系数。根据大量研究表明,S1000在弯曲加载时近似等于90%的极限抗拉强度Su,而在轴向加载时近似等于75%的极限抗拉强度Su,在扭转加载时,其近似等于90%的极限剪切强度Sus。如果考虑疲劳数据统计的分散性,则需要在规定可靠度水平的中值基准S-N数据的基础上,对零件的疲劳强度进行修正,在缺乏严格统计分析数据时,可以参见表3.3所示的可靠度系数进行修正。
表3.3 可靠度系数

由S-N曲线的特点可知,在疲劳强度达到永久极限寿命时,随着N的增加,Sbe的值基本趋于稳定,疲劳试验不可能无限进行下去,必须规定一个循环次数,达到该值就停止试验,而这个无失效的疲劳应力幅被称为疲劳极限。前人根据大量的试验观察到了一个现象,锻钢的疲劳极限与材料抗拉强度之间存在着一种关系

铸铁的弯曲疲劳极限一般定为5×107次循环,对应为0.4倍的极限抗拉强度。铝合金一般规定为5×108次循环,一般取在0.4倍的极限抗拉强度,对于铝合金抗拉强度超过336MPa时,疲劳极限取130MPa。