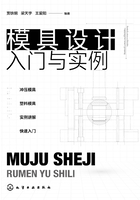
1.1 冲裁模具的设计从哪开始
在冲裁模具设计中有个非常重要的零件与产品相同或相似,这个零件叫作凸模、凹模,所以要先设计出凸模、凹模。但仅仅有凸模、凹模不行,还需要有定位零件、卸料与出件零件、导向零件、支承与固定零件等等,才能确保模具保质保量地加工出所需的产品。所以模具的设计从凸模、凹模刃口尺寸的计算开始。
1.1.1 冲裁模具凸、凹模刃口尺寸的计算
(1)冲裁件的质量
冲裁变形过程经过弹性变形阶段、塑性变形阶段、断裂分离阶段。最后冲裁件由凸模和凹模相互挤压,使落料件挤进凹模、冲孔件挤在凸模上,最后产生裂纹分离开,如图1⁃1所示。

图1⁃1 冲裁变形过程
冲裁件的质量包括冲裁件的断面状况[如图1⁃2(a)所示]、尺寸精度和形状误差的要求。尺寸精度和形状误差基本与机械加工零件一样,但其断面如图1⁃2(b)所示,不如机械加工零件那样有棱有角、表面可以做到光洁。而且冲裁件由于冲裁变形过程形成的断面明显呈现出四个特征区,即圆角、光亮带、断裂带和毛刺。

图1⁃2 冲裁件的断面状况
(2)影响冲裁件断面特征的因素
① 板料的性能对断面质量的影响 塑性好的板料,冲裁时由于裂纹出现得较迟,板料被剪切挤压的深度较大,因而光亮带所占比例大,断裂带较小,但圆角、毛刺也较大;而塑性差的板料,断裂倾向严重,裂纹出现得较早,使得光亮带所占比例小,断裂带较大,但圆角和毛刺都较小。
② 冲裁间隙对断面质量的影响
a.当间隙合理时,如图1⁃3(a)所示,凸模刃口处的裂纹相对凹模刃口处的裂纹重合,光亮带较大,断裂带较小,且圆角、毛刺也较小,断面质量理想,如图1⁃3(b)所示。

图1⁃3 间隙合理
b.当间隙过小时,如图1⁃4(a)所示,凸模刃口处的裂纹相对凹模刃口处的裂纹向外错开,上、下裂纹不重合,板料在上、下裂纹相距最近的地方将发生第二次剪裂,上裂纹表面压入凹模时受到凹模壁的压挤产生第二光亮带或断续的小光亮块,断面质量不理想,如图1⁃4(b)所示。而且第二光亮带隐藏裂纹,如图1⁃4(c)所示,使用一段时间第二光亮带脱落后会与图1⁃5(b)相似。

图1⁃4 间隙过小
c.当间隙过大时,如图1⁃5(a)所示,凸模刃口处的裂纹相对凹模刃口处的裂纹向内错开,上、下裂纹不重合,塑性变形阶段较早结束,致使断面光亮带减小,断裂带增大,且圆角、毛刺也较大,断面质量不理想,如图1⁃5(b)所示。

图1⁃5 间隙过大
d.间隙不均匀时,实际使用中,因安装调整等原因使得凸模与凹模间隙不均匀,冲裁件断面状况如图1⁃6所示,光亮带不均匀。

图1⁃6 间隙不均匀
(3)冲裁模具凸模、凹模合理间隙的选择
冲裁间隙是影响冲裁件断面质量的主要因素,冲裁间隙还影响着模具寿命、冲裁力(包括卸料力、顶件力、推件力)、冲裁件的尺寸精度,因此冲裁间隙是冲裁模具设计中一个非常重要的工艺参数。
① 凸模与凹模之间的间隙 凸模与凹模间每侧的间隙称为单面间隙,用Z/2表示;两侧间隙之和称为双面间隙,用Z表示 。
冲裁间隙的数值等于凸、凹模刃口尺寸的差值,如图1⁃7所示,即
Z=Dd-dp(1⁃1)
式中 Dd——凹模刃口尺寸;
dp——凸模刃口尺寸。

图1⁃7 冲裁间隙
② 间隙对冲裁力的影响 如图1⁃8所示,间隙很小时,因板料的挤压和摩擦作用增强,冲裁力必然较大。

图1⁃8 板料挤压和凹模侧向挤压
③ 间隙对模具寿命的影响 在冲裁过程中,板料对模具作用力主要集中在凸、凹模刃口部分。如果间隙小,垂直冲裁力和侧向挤压力将增大(见图1⁃8),摩擦力也增大,所以小间隙将使凸、凹模刃口磨损加剧。小间隙因落料件堵塞在凹模洞口的胀力较大,容易产生凹模胀裂。小间隙还易产生小凸模折断等异常现象。
④ 冲裁间隙值的确定 冲裁间隙对冲裁件质量、冲压力、模具寿命等都有很大的影响,但由于影响的规律各有不同。因此,并不存在一个绝对合理的间隙值,能同时满足冲裁件断面质量最佳、尺寸精度最高、冲模寿命最长、冲压力最小等各方面的要求。在冲压实际生产中,为了获得合格的冲裁件 、较小的冲压力和保证模具有一定的寿命,给间隙值规定一个范围,这个间隙值范围就称为合理间隙,这个范围的最小值称为最小合理间隙(Zmin),最大值称为最大合理间隙(Zmax)。考虑到冲模在使用过程中会逐渐磨损,间隙会增大,故在设计和制造新模具时,应采用最小合理间隙。
目前没有一个完全准确的间隙,既能保证冲裁件断面理想,又能使冲裁力小、模具寿命高来供设计者选择,因此合理间隙只能选择一个范围。
(4)确定合理间隙的方法
① 理论确定法 理论确定法的主要依据是保证凸、凹模刃口处产生的上 、下裂纹相互重合,以便获得良好的断面质量。图1⁃9所示为冲裁过程中开始产生裂纹的瞬时状态,根据图中的几何关系,可得合理间隙Z的计算公式为:
Z=2t(1-h0/t)tanβ(1⁃2)

图1⁃9 合理间隙的确定
式中 t——板料厚度;
h0——产生裂纹时凸模挤入材料的深度;
h0/t——产生裂纹时凸模挤入材料的相对深度;
β——剪裂纹与垂线间的夹角。
由式(1⁃2)可以看出,合理间隙与板料厚度t、相对挤入深度h0/t及裂纹角β有关,而h0/t与β又与板料性质有关,见表1⁃1。
表1⁃1 h0/t与β值

理论计算法在生产中使用不方便,主要用来分析间隙与上述几个因素之间的关系。因此,实际生产中广泛采用查表法来确定间隙值。
② 查表法 按材料的性能和厚度来选择冲裁间隙。尺寸精度和断面质量要求较高的冲裁件选择表1⁃2,要求不高的冲裁件选择表1⁃3。
表1⁃2 冲裁模初始双面间隙Z(一)mm


续表

注:本表适用于尺寸精度和断面质量要求较高的冲裁件。
表1⁃3 冲裁模初始双面间隙Z(二)mm

注:1.冲裁皮革、石棉和纸板时,间隙取08钢的25% 。
2.本表适用于尺寸精度和断面质量要求不高的冲裁件。
确定合理间隙无论是理论确定法还是查表法,影响间隙值的主要因素是板料性质和厚度。厚度愈大、塑性愈差的板料,其合理间隙值就愈大;反之,厚度愈薄、塑性愈好的板料,其合理间隙值就愈小。
(5)凸、凹模刃口尺寸计算的原则
在冲裁变形过程中,凸模将分离的板料推入凹模洞口,如图1⁃10所示,落料件和冲孔件的区别在于所需要的产品形状,落料件如图1⁃10(a)的光面是因凹模刃口挤切材料产生的,而冲孔件如图1⁃10(b)的光面是凸模刃口挤切材料产生的。在冲裁件尺寸的测量和使用中,都是以光面的尺寸为基准。

图1⁃10 冲裁变形过程
所以,在计算刃口尺寸时,应按落料和冲孔两种情况分别考虑,其原则如下:
① 落料时 因落料件光面尺寸与凹模刃口尺寸相等或基本一致,应先确定凹模刃口尺寸,落料凸模的基本尺寸则是在凹模基本尺寸上减去最小合理间隙 。
② 冲孔时 因孔的光面尺寸与凸模刃口尺寸相等或基本一致,应先确定凸模刃口尺寸,冲孔凹模的基本尺寸则是在凸模基本尺寸上加上最小合理间隙。
③ 凸、凹模刃口的制造公差 应根据冲裁件的尺寸公差和凸、凹模加工方法确定,既要保证冲裁间隙要求和冲出合格零件,又要便于模具加工。
(6)凸模、凹模刃口尺寸的计算
① 经验确定法 如图1⁃11所示圆垫,材料为10钢,厚度t=2mm。对凸凹模刃口尺寸(见图1⁃12)如何确定进行分析。

图1⁃11 圆垫

图1⁃12 凸凹模刃口尺寸
a.圆垫属于落料件,应先确定凹模刃口尺寸Dd,冲裁件合格尺寸范围29.8~30mm。10钢含碳量wc=0.10%,属于软钢,查表1⁃2得,Zmin=0.12mm,Zmax=0.16mm。凸模与凹模刃口的制造公差之和=Zmax-Zmin=0.16-0.12=0.04mm。凸模相对容易加工,凸模的制造公差为0.016mm,凹模刃口的制造公差为0.024mm。
b.取冲裁件最大尺寸,则凹模刃口尺寸Dd为30mm,刚开始冲裁时,得到的冲裁件也符合要求,但是凹模刃口与冲裁件有摩擦,冲裁一段时间,凹模刃口尺寸Dd由于磨损而变大,再生产的冲裁件就不合格了。
c.取冲裁件最小尺寸,则凹模刃口尺寸Dd为29.8mm,凹模刃口尺寸D磨损量有0.2mm,可满足使用要求,但距公称尺寸30mm,冲出的件显得有些小了。
d.取冲裁件平均尺寸,则凹模刃口尺寸Dd为29.9mm,凹模刃口尺寸Dd磨损量有0.1mm,可满足使用要求,凹模刃口尺寸Dd的制造公差上偏差为+0.024mm,下偏差为0mm,如果凹模刃口尺寸Dd加工成上偏差为29.924mm,生产的冲裁件也是合格的,磨损量也有0.076mm。满足生产要求。
落料凸模刃口Dp=29.9-0.12=29.78mm,制造公差上偏差为0mm,下偏差为-0.016mm。
由于图1⁃11所示圆形冲裁件比较简单,用以上经验分析可以确定凸凹模刃口尺寸,但如果冲裁件比较复杂,还要考虑凹模刃口尺寸冲裁过程的磨损、加工过程中的制造公差,凸凹模之间的合理间隙,以及冲裁件的制造公差,因此总结出了以下两种凸凹模刃口尺寸计算方法和计算公式。
② 凸模、凹模刃口尺寸的计算法
a.凸、凹模分别加工时的计算方法。凸、凹模分别加工是指凸模与凹模分别按各自图样上标注的尺寸及公差进行加工,冲裁间隙由凸、凹模刃口尺寸及公差保证。这种方法要求凸模和凹模的刃口尺寸都要计算出来并标注公差。
设落料件外形尺寸为,冲孔件内孔尺寸为
,根据刃口尺寸计算原则,可得如下。
落料。应先确定凹模刃口尺寸Dd,落料凸模刃口尺寸Dp则是在凹模刃口尺寸Dd上减去最小合理间隙。
Dd=(Dmax-xΔ(1⁃3)
Dp=(Dd-Zmin
=(Dmax-xΔ-Zmin(1⁃4)
冲孔。应先确定凸模刃口尺寸dp,冲孔凹模刃口尺寸dd则是在凸模基本尺寸上加上最小合理间隙。
dp=(dmin+xΔ(1⁃5)
dd=(dp+Zmin
=(dmin+xΔ+Zmin(1⁃6)
式中 Dd,Dp——落料凹、凸模刃口尺寸,mm;
dp,dd——冲孔凸、凹模刃口尺寸,mm;
Dmax——落料件的最大极限尺寸,mm;
dmin——冲孔件孔的最小极限尺寸,mm;
Δ——冲裁件的制造公差(若冲裁件为自由尺寸,可按IT12~IT14级精度处理),mm;
Zmin——最小合理间隙,mm;
δp,δd——凸、凹模制造公差mm,按“入体”原则标注,即凸模为轴类按单向负偏差标注,凹模为孔类按单向正偏差标注;
x——磨损系数,x值在0.5~1之间,它与冲裁件精度有关,可查表1⁃4或按下列关系选取:
冲裁件精度为IT10以上时,x=1;
冲裁件精度为IT11~IT13时,x=0.75;
冲裁件精度为IT14以下时,x=0.5。
表1⁃4 磨损系数x

根据上述计算公式,可以将冲裁件与凸、凹模刃口尺寸及公差的分布状态用图1⁃13表示。从图中还可以看出,无论是冲孔还是落料,为了保证间隙值,凸、凹模的制造公差相加之和必须满足下列条件:
δp+δd≤Zmax-Zmin(1⁃7)
可以取δp=0.4(Zmax-Zmin),δd=0.6(Zmax-Zmin),也可以各分配50%,即δp=0.5(Zmax-Zmin),δd=0.5(Zmax-Zmin)。

图1⁃13 落料、冲孔时各部分尺寸及公差的分布状态
当在同一工步冲出冲裁件上两个以上孔时,因凹模磨损后孔距尺寸不变,故凹模型孔的中心距可按(1⁃8)式确定:
Ld=(Lmin+0.5Δ)±Δ/8(1⁃8)
式中 Ld——凹模型孔中心距,mm;
Lmin——冲裁件孔心距的最小极限尺寸,mm;
Δ——冲裁件孔心距公差,mm 。
当冲件上有位置公差要求的孔时,凹模上型孔的位置公差一般可取冲裁件位置公差的1/3~1/5 。
b.凸、凹模配作加工时的计算方法。凸、凹模配作加工是指先按图样设计尺寸加工好凸模或凹模中的一件作为基准件(一般落料时以凹模为基准件,冲孔时以凸模为基准件),然后根据基准件的实际尺寸按间隙要求配作另一件。采用凸、凹模配作法加工时,只需计算基准件的刃口尺寸及公差,并详细标注在设计图样上。而另一非基准件不需计算,且设计图样上只标注基本尺寸(与基准件基本尺寸对应一致),不注公差,但要在技术要求中注明:“凸(凹)模刃口尺寸按凹(凸)模实际刃口尺寸配作,保证双面间隙值为Zmin~Zmax”。
根据冲裁件的结构形状不同,刃口尺寸的计算方法如下:
落料。落料时以凹模为基准,配作凸模。设落料件的形状与尺寸如图1⁃14(a)所示,图1⁃14(b)为落料凹模刃口的轮廓图,图中虚线表示凹模磨损后尺寸的变化情况。

图1⁃14 落料件与落料凹模
从图1⁃14(b)可看出,凹模磨损后刃口尺寸的变化有增大、减小和不变三种情况,故凹模刃口尺寸也应分三种情况进行计算:凹模磨损后变大的尺寸(如图中A类尺寸),按一般落料凹模尺寸公式计算;凹模磨损后变小的尺寸(如图中B类尺寸),因它在凹模上相当于冲孔凸模尺寸,故按一般冲孔凸模尺寸公式计算;凹模磨损后不变的尺寸(如图中C类尺寸),可按凹模型孔中心距尺寸公式计算。具体计算公式见表1⁃5。
冲孔。冲孔时以凸模为基准,配作凹模。设冲件孔的形状与尺寸如图1⁃15(a)所示,图1⁃15(b)为冲孔凸模刃口的轮廓图,图中虚线表示凸模磨损后尺寸的变化情况。
表1⁃5 以落料凹模为基准的刃口尺寸计算

注:Ad、Bd、Cd——落料凹模刃口尺寸;A、B、C——落料件的基本尺寸;Amax、Bmin、Cmin——落料件的极限尺寸;Δ——落料件的公差;x——磨损系数。

图1⁃15 冲件孔与冲孔凸模
从图1⁃15(b)中看出,冲孔凸模刃口尺寸的计算同样要考虑三种不同的磨损情况:凸模磨损后变大的尺寸(如图中a类尺寸),因它在凸模上相当于落料凹模尺寸,故按一般落料凹模尺寸公式计算;凸模磨损后变小的尺寸(如图中b类尺寸),按一般冲孔凸模尺寸公式计算;凸模磨损后不变的尺寸 (如图中c类尺寸)仍按凹模型孔中心距尺寸公式计算。具体计算公式见表1⁃6。
表1⁃6 以冲孔凸模为基准的刃口尺寸计算

注:ad、bd、cd——冲裁孔凸模刃口尺寸;a、b、c——冲裁件孔的基本尺寸;amax、bmin、cmin——冲裁件孔的极限尺寸;Δ——冲裁件孔的公差;x——磨损系数。
1.1.2 冲裁模具的设计基准的选择
(1)模具凸模、凹模刃口尺寸计算方法的选用举例
例如:圆垫如图1⁃11所示,计算模具凸模、凹模刃口尺寸。
① 用分开加工法计算模具凸模、凹模刃口尺寸。
圆垫属于落料件,凹模磨损后变大的尺寸,则由式(1⁃3)得:
Dd=(Dmax-xΔ
Dp=(Dd-Zmin
查表1⁃3得,x=0.5。
由式(1⁃7)得,δp=0.5(Zmax-Zmin),δd=0.5(Zmax-Zmin)。
将已知和查表的数据代入公式,即得
Dd=(30-0.5×0.2=29.
mm
Dp=(29.9-0.12=29.7
mm
与经验确定法的结果基本一致。
② 用配作加工法计算模具凸模、凹模刃口尺寸。
圆垫属于落料件,凹模磨损后变大的尺寸,则表1⁃4得:
Ad=(Amax-xΔ
查表1⁃3得,x=0.75。
将已知和查表的数据代入公式,即得
Ad=(30-0.5×0.2=29.
落料凸模刃口尺寸按凹模实际刃口尺寸配作,保证双面间隙值0.12~0.16mm。
③ 凸凹模刃口尺寸计算方法比较分析。
a.根据冲裁件的最大最小尺寸来确定凸凹模刃口尺寸和制造公差,可行而且简单,但是涉及到冲裁件的安装、配合部位的尺寸,需要和冲裁件的设计者协商确定。
b.分别加工法计算中,本来冲裁件精度不高,其制造公差Δ在0.2mm以上,但却要求凸或凹模的制造公差在0.02mm以内,并且用凸、凹模的制造公差保证凸、凹模的冲裁间隙,即δd+δp≤Zmax-Zmin。如果凸模或凹模的制造公差稍大些,就会使凸、凹模的冲裁间隙或大于最大合理间隙Zmax或小于最小合理间隙Zmin。优点是互换性好,便于成批制造,适用于圆形、矩形等简单形状的冲裁件。
c.配作加工法中的凸模或凹模的制造公差为0.05mm比分别加工法的0.02mm放大了很多。配作加工是先加工一个件,通过测量已加工好件的尺寸再配另一个件,冲裁间隙由配作保证,工艺比较简单,制造相对容易。缺点是互换性不好,适用于冲裁薄板件(因其Zmax-Zmin很小)和复杂形状件的冲模加工。
由于机床的加工精度越来越高,分别加工法要求凸、凹模的制造公差较小也不成问题,在实际生产中采用哪种方法还要看具体实际情况。
(2)模具的设计基准的选择
如图1⁃16所示,冲裁模具设计基准选择在凸模、凹模刃口尺寸确定后,以凸模、凹模刃口尺寸为设计基准。往上是凸模的安装和固定,以及凸模上卸料、上模与压力机滑块的安装等结构设计;往下是凹模的安装和固定、下模与压力机工作台的安装等结构设计;往左、往右是导柱和导套、固定螺栓、卸料螺栓、销钉的结构设计。

图1⁃16 冲裁模具设计基准选择
1—凸模;2—凹模