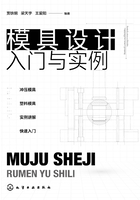
1.3 怎样选择模具零件结构设计
1.3.1 工作零件设计
(1)凸模
凸模的基本结构均由是安装部分、工作部分组成,对于细小凸模增加过渡部分增加强度,如图1⁃31所示。

图1⁃31 凸模的基本结构
1—安装部分;2—过渡部分;3—工作部分
① 圆形凸模 刃口为圆形凸模的结构及固定如图1⁃32所示。

图1⁃32 圆形凸模的结构及固定
② 非圆形凸模 如图1⁃33所示,刃口为非圆形凸模,为防止转动,增设防止转动螺栓、圆柱销钉、平键等。

图1⁃33 非圆形凸模的结构及固定

图1⁃34 冲小孔凸模及其导向结构
1—冲小孔凸模;2—凸模固定板;3—导向护套;4—卸料板
③ 冲小孔凸模 冲小孔是指孔径d小于被冲板料的厚度或直径d<1mm的圆孔和面积A<1mm2的孔。由于冲小孔的凸模强度和刚度差,容易弯曲和折断,所以必须采取措施提高凸模的强度和刚度,如图1⁃34所示,利用卸料板做导向或增加导向护套,为了保证卸料板具有导向作用,可采用刚性卸料板。采用弹性卸料板时需要单独增设导向装置。
(2)凹模
① 凹模的外形结构与固定方法 如图1⁃35所示,刃口为圆形可采用图1⁃35(a)、(b)、(c)固定结构,刃口为非圆形可采用图1⁃35(c)、(d)防止转动固定结构。图1⁃35(d)的A向视图如图1⁃36所示,采用螺栓、圆柱销、平键防止凹模转动。

图1⁃35 凹模形式及其固定

图1⁃36 防止凹模转动
② 凹模刃口的结构形式 冲裁凹模刃口形式有直筒形和锥形两种。表1⁃12列出了冲裁凹模刃口的形式,可供设计选用时参考。
表1⁃12 冲裁凹模的刃口形式

③ 凹模轮廓尺寸的确定 凹模轮廓尺寸包括凹模板的平面尺寸L×B(长×宽)及厚度尺寸H。从凹模刃口至凹模外边缘的最短距离称为凹模的壁厚c。对于简单对称形状刃口的凹模,由于压力中心即为刃口对称中心,所以凹模的平面尺寸即可沿刃口型孔向四周扩大一个凹模壁厚来确定,如图1⁃37(a)所示,即
L=l+2c B=b+2c(1⁃30)
式中 l——沿凹模长度方向刃口型孔的最大距离,mm;
b——沿凹模宽度方向刃口型孔的最大距离,mm;
c——凹模壁厚,mm,主要考虑布置螺孔与销孔的需要,同时也要保证凹模的强度和刚度,计算时可参考表1⁃13选取。
对于多型孔凹模,如图1⁃37(b)所示,设压力中心O沿矩形l×b的宽度方向对称,而沿长度方向不对称,则为了使压力中心与凹模板中心重合,凹模平面尺寸应按式(1⁃31)计算:
L=l'+2c B=b+2c(1⁃31)
式中 l'——沿凹模长度方向压力中心至最远刃口间距的2倍,mm。

图1⁃37 凹模轮廓尺寸的计算
凹模板的厚度主要是从螺钉旋入深度和凹模刚度的需要考虑的,一般应不小于8mm。随着凹模板平面尺寸的增大,其厚度也应相应增大。
表1⁃13 凹模壁厚cmm

注:1.冲件料薄时取表中较小值,反之取较大值;
2.型孔为圆弧时取小值,为直边时取中值,为尖角时取大值。
整体式凹模板的厚度可按式(1⁃32)估算:
H=K1K2(1⁃32)
式中 F——冲裁力,N;
K1——凹模材料修正系数,合金工具钢取K1=1,碳素工具钢取K1=1.3;
K2——凹模刃口周边长度修正系数,可参考表1⁃14选取。
表1⁃14 凹模刃口周边长度修正系数K2

以上算得的凹模轮廓尺寸L×B×H,当设计标准模具或虽然设计非标准模具,但凹模板毛坯需要外购时,应将计算尺寸L×B×H按冲模国家标准中凹模板的系列尺寸进行修正,取接近的较大规格的尺寸。
1.3.2 定位零件设计
(1)挡料销
挡料销的作用是来挡住条料搭边或冲件轮廓以限定条料送进的距离。根据挡料销的工作特点及作用分为固定挡料销、活动挡料销和始用挡料销。
① 固定挡料销 如图1⁃38(a)所示,可根据搭边的大小选择固定挡料销,如果距离凹模刃口距离e过近,可加工成图1⁃38(b)所示结构。

图1⁃38 固定挡料销
② 活动挡料销 如图1⁃39所示。

图1⁃39 活动挡料销
③ 始用挡料销 如图1⁃40所示,始用挡料销在条料开始送进时,用手压住始用挡料销,使始用挡料销伸出导料板挡住条料起定位作用。然后松开手,在弹簧作用下始用挡料销缩进导料板内不起挡料作用,始用挡料销一般用于条料以导料板导向的级进模(见图1⁃26),采用始用挡料销的目的是为了提高材料的利用率。

图1⁃40 始用挡料销
(2)导料销、导料板
导料销与挡料销结构一样,作用是保证条料沿正确的方向送进。导料销一般设两个,并位于条料的同一侧。导料板的作用与导料销相同,其结构有两种,如图1⁃41所示。

图1⁃41 导料板结构
(3)导正销
使用导正销一般是前一个工位在板料上冲一个定位工艺孔(或产品上的孔),接着下一个工位就是利用导正销导正(见图1⁃42),保证冲件在不同工位上冲出的内形与外形之间的相对位置公差要求。
导正销结构形式如图1⁃42所示,一般分为锐角如图1⁃43(a)、R形如图1⁃43(b)和锥形如图1⁃43(c)。

图1⁃42 导正销导正
1—凸模;2—导正销;3—板料

图1⁃43 导正销结构形式
导正销的头部由圆锥形的导入部分和圆柱形的导正部分组成,故导正部分的直径可按式(1⁃33)计算:
d=dp-a(1⁃33)
式中 d——导正销导正部分直径,mm;
dp——导正孔的冲孔凸模直径,mm;
a——导正销直径与冲孔凸模直径的差值,mm,可参考表1⁃15选取。
导正部分的直径公差可按h6~h9选取。导正部分的高度一般取h=(0.5~1)t,或按表1⁃16选取。
表1⁃15 导正销与冲孔凸模间的差值amm

表1⁃16 导正销导正部分高度hmm

由于导正销常与挡料销配合使用,挡料销只起粗定位作用,所以挡料销的位置应能保证导正销在导正过程中条料有被前推或后拉少许的可能。挡料销与导正销的位置关系如图1⁃44所示。

图1⁃44 挡料销与导正销的位置关系
按图1⁃44(a)方式定位时,挡料销与导正销的中心距为:
s1=s-Dp/2+D/2+0.1(1⁃34)
按图1⁃44(b)方式定位时,挡料销与导正销的中心距为:
s'1=s+Dp/2-D/2-0.1(1⁃35)
式中 s1、s'1——挡料销与导正销的中心距,mm;
s——送料进距,mm;
Dp——落料凸模直径,mm;
D——挡料销头部直径,mm。
(4)侧压装置
如图1⁃45所示。在一副模具中,侧压装置的数量和设置位置视实际需要而定。但对于板料厚度较薄(一般为t<0.3mm)或材料较软的板料,容易造成条料挤压变形,宜采用辊轴自动送料装置。

图1⁃45 侧压装置
1—导料板;2—弹簧式侧压装置;3—条料
(5)导向顶料销
两侧顶起顶料销如图1⁃46所示,当卸料板随着上模抬起,弹簧带动导向顶料销将条料或带料的边缘顶起,向前送进。导向顶料销具有顶料和导向作用。

图1⁃46 导向顶料销
1—卸料板;2—导向顶料销;3—凹模板;4—弹簧;5—下模座
导向顶料销尺寸设计如图1⁃47所示,其中:
h1=0.5d(1⁃36)
H1=h1+0.5(1⁃37)
H2=t+1.5(1⁃38)
式中 h1——导向顶料销头部高度,mm;
d——导向顶料销直径,mm;
H1——卸料板沉孔深度,mm;
H2——导向顶料销槽宽,mm;
t——条料或带料厚度,mm。

图1⁃47 导向顶料销结构形式
中间顶起顶料销如图1⁃48所示,用于条料或带料中间的弹起。

图1⁃48 中间顶起顶料销
1—顶料销;2—导料板;3—凹模固定板;4—下模座
1.3.3 卸料与出件装置设计
卸料与出件装置的作用是当冲模完成一次冲压之后,把冲件或废料从模具工作零件上卸下来,以便冲压工作继续进行。通常,把冲件或废料从凸模上卸下称为卸料,把冲件或废料从凹模中卸下称为出件。常用的弹性卸料装置的结构形式如图1⁃49所示。

图1⁃49 弹性卸料装置
1—卸料板;2—弹性元件;3—卸料螺钉
弹性卸料板的平面外形尺寸等于或稍大于凹模板尺寸,厚度取凹模厚度的0.6~0.8倍。在级进模中,特别小的冲孔凸模与卸料板的双边间隙可取0.3~0.5 mm。当卸料板对凸模起导向作用时,卸料板与凸模间按H7/h6配合。此外,为便于可靠卸料,在模具开启状态时,卸料板工作平面应高出凸模刃口端面0.3~0.5mm。
卸料螺钉一般采用标准的阶梯形螺钉,其数量按卸料板形状与大小确定,卸料板为圆形时常用3~4个,为矩形时一般用4~6个。卸料螺钉的直径根据模具大小可选8~12mm,各卸料螺钉的长度应一致,以保证装配后卸料板水平和均匀卸料。
弹性卸料装置可装于上模或下模,依靠弹簧或橡皮的弹力来卸料,卸料力不太大,但冲压时可兼起压料作用,故多用于冲裁料薄及平面度要求较高的冲件。弹簧或橡胶选择如下:
(1)弹簧
模具卸料常用的弹簧为圆柱螺旋压缩弹簧,弹簧丝截面有圆形和矩形,矩形截面圆柱螺旋压缩弹簧与圆形截面螺旋压缩弹簧相比,其特性曲线更接近于直线,即弹簧的刚度更接近固定的常数,方向和定位性好。弹簧的选用包括如下内容:
① 选择弹簧压力:
F预≥(1⁃39)
式中 F预——弹簧的预压力,N;
F卸——卸料力,N;
n——弹簧根数。
② 选择弹簧压缩量:
h总≥h预+ h工作+ h修磨(1⁃40)
式中 h总——弹簧总的压缩量,mm;
h预——弹簧的预压缩量,mm;
h工作——卸料板的工作行程,mm,对于冲裁模取板料厚度+2mm;
h修磨——模具的修磨量或调整量,mm,一般取4~6mm。
(2)橡胶
橡胶作为卸料装置中的弹性元件,具有简单、经济等特点,被大量使用在冲压模具中。橡胶允许承受的负荷比弹簧大,且安装方便。
橡胶产生的压力F由式(1⁃41)得出:
F=A×p(1⁃41)
式中 A——橡胶的承受面积,mm2;
p——与橡胶压缩量有关的单位压力,MPa,可查表1⁃17。
表1⁃17 橡胶压缩量与单位压力关系

为了保证橡胶的正常使用,不至于过早失去弹性,最大压缩量h总不能超过其自由高度h自由的35%~45%,预压缩量h预一般为橡胶自由高度h自由的10%~15%。最大压缩量h总为橡胶的工作行程h工作与预压缩量h预之和,则橡胶的工作行程h工作为:
h工作=h总-h预=(25%~30%)h自由(1⁃42)
式中 h总——橡胶的最大压缩量,mm;
h预——橡胶的预压缩量,mm;
h工作——卸料板的工作行程,mm,对于冲裁模取板料厚度+1mm(凸模进入凹模)+1mm(上模抬起凸模在卸料板内)。
考虑到模具的修磨量或调整量(h修磨=4~6mm),所以橡胶的自由高度h自由为:
h自由=+h修磨=(3.5~4.0)h工作+h修磨(1⁃43)
为了橡胶具有一定的弹性和稳定性,圆形橡胶的高度h与直径D之比须满足式(1⁃44):
0.5≤h/D≤1.5(1⁃44)
如果超过1.5,应将橡胶分段,每段之间垫上钢垫圈,并使每段的h/D值仍在上述范围内。
非标准形状橡胶的大小凭经验根据模具卸料的空间合理布置,周围留有足够的空间,允许橡胶压缩时断面尺寸的胀大。往往在模具装配和试模后,增减橡胶数量、改进橡胶形状。
选用橡胶时的步骤:
① 根据工作行程h工作计算橡胶的自由高度h自由;
② 根据自由高度h自由计算橡胶预压缩后的装配高度h装配:
h装配=h自由-h预(1⁃45)
③ 根据模具卸料的空间确定橡胶的断面面积。
(3)出件装置
出件装置的作用是从凹模内卸下冲件或废料。为了便于学习,把装在上模内的出件装置称为推件装置,装在下模内的称为顶件装置。
① 推件装置 推件装置有刚性推件装置和弹性推件装置两种。图1⁃50所示为刚性推件装置。

图1⁃50 刚性推件装置
1—打杆;2—模柄;3—推件块
图1⁃51所示为弹性推件装置。

图1⁃51 弹性推件装置
1—弹性元件;2—推板;3—连接推杆;4—推件块
② 顶件装置 顶件装置一般是弹性的,其基本零件是顶件块、顶杆和弹顶器,如图1⁃52所示。弹顶器可做成通用的,其弹性元件可以是弹簧或橡胶。

图1⁃52 弹性顶件装置
1—顶件块;2—顶杆;3—橡胶
1.3.4 模架及其零件设计
(1)模架
模架是上、下模座与导向零件的组合体,如图1⁃53所示,有对角导柱模架、后侧导柱模架、中间导柱模架、四导柱模架等,可根据模具结构进行选择,也可以自行设计。

图1⁃53 标准模架
(2)导向零件
① 滑动式导柱导套结构(见图1⁃54) 加工、装配方便,应用最广泛,但导向精度不如滚动式。导柱、导套材料可选用T8、T10、Cr12、Cr12MoV等材料,或采用20钢表面渗碳,热处理硬度55~60HRC。

图1⁃54 导柱导套与模架配合关系
1—上模座;2—导套;3—导柱;4—下模座
② 滚动式导柱导套结构
a.滚珠式(见图1⁃55)。通过滚珠与导套实现有微量过盈的无间隙配合(一般过盈量为0.01~0.02mm),导向精度高,使用寿命长,但结构较复杂,制造成本高,主要用于精密冲裁模、硬质合金冲裁模、高速冲模及薄材料的冲裁模具。滚动导柱、导套材料可选用GCr15钢,热处理硬度56~62HRC。

图1⁃55 滚珠式导柱导套结构
1—导套;2—保持架;3—滚珠;4—导柱
b.滚针式(见图1⁃56)。用于极薄金属与树脂材料的高精度冲裁模具,如引线框架、印刷电路板、软板等冲裁模具。

图1⁃56 滚针式导柱导套结构
1—导柱;2—保持架;3—滚针轴承;4—导套
1.3.5 支承与固定零件设计
(1)模柄
如图1⁃57(a)所示,模柄安装在上模座上,其作用是把上模固定在压力机滑块上,同时使模具中心通过滑块的压力中心。一般在小型模具上都是通过模柄与压力机滑块相连接的。为了适应不同压力机上滑块模柄孔尺寸的需要,设计模柄套如图1⁃57(b)所示。

图1⁃57 模柄的安装形式
1—模柄;2—模柄套;3—上模座
对于大中型冲压模具的固定,如图1⁃58所示。由于模具重量大,采用模柄形式难以承受模具上模的重量,需要采用螺栓直接固定或加垫块、压板将模具的上下模分别固定在压力机滑块和工作台(或垫板上)。

图1⁃58 大型冲压模具的固定
(2)凸模(凹模)固定板与垫板
如图1⁃59所示,凸模(凹模)固定板与垫板外形尺寸一致,厚度可取凹模厚度的60%~80%。固定板与凸模或凹模为H7/n6或H7/m6配合。
垫板的作用是承受并扩散凸模或凹模传递的压力,以防止模座被挤压损伤。垫板材料一般为45钢,热处理硬度40~45HRC,厚度可取3~20mm。

图1⁃59 凸模(凹模)固定板与垫板
1—垫板;2—凸模;3—凸模固定板;4—刚性(固定)卸料板;5—凹模固定板;6—凹模