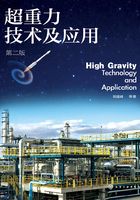
2.3 旋转填充床内流体停留时间实验测定
了解液体在转子内停留时间和返混程度,对于传质与反应的研究具有至关重要的意义。美国Case Western Reserve大学的Keyvany[14]等前人采用脉冲示踪的方法,通过在液体的进口处和转子外空腔中分别安装电导探头来测定停留时间分布。然而,这包括了液体在进出口管路中的停留与返混,并非填料内的停留时间分布规律。北京化工大学郭锴等[1]将电导探头固定于旋转转子上,进行原始测量,测得液体在转子填料内,不含液体在外腔空间飞行的停留时间,可真实反映液体在填料中停留时间分布。
2.3.1 实验方法
由于液体在转子内的停留时间很短,在毫秒级,人工取样测量已经不可能满足要求。应用计算机数据采集系统,同时对进出口物料进行测量,方能达到目的。实验采用脉冲示踪的方法,在旋转填充床稳定操作时脉冲加入示踪物质,在转子内外径处同时测量液体电导率的变化,然后进行数学处理,得到停留时间分布规律。
典型停留时间分布曲线见图2-31。图中两条曲线的高度即电导率的绝对值,没有实际意义,因为这一数值与基线(即清水的电导率)有关,而在各次实验中,水的电导率可能是不同的,这一数值也和电导探头的灵敏度、沾污程度及电导仪参数的设定有关。为了在图上看得更清楚,将两条曲线的基线拉开以示区别。两条曲线在横坐标(时间)上位置的绝对值同样不具有实际意义,这一数值取决于自数据采集开始到进样的时间间隔。这个时间间隔是手工控制的,大约在0.5s左右。通过停留时间分布曲线,需要得到的是两个峰的间隔和峰的宽度,它们分别代表了平均停留时间和方差。各次采样时间间隔均相同且为9.3ms,多数实验点采样300次。

图2-31 停留时间分布曲线
对进口和出口两条曲线分别用式(2-44)和式(2-45)计算平均停留时间和方差。进、出口曲线平均停留时间之间的差即为液体在填料转子内的平均停留时间。


式中 ——平均停留时间,s;
E(t)——停留时间密度函数,s-1;
t——时间,s;
σ2t——方差,。
在图2-31中,进口曲线的锯齿形波纹代表了对填料内缘上某一固定点每转一周示踪物淋洒一次。这意味着,在填料内缘附近存在着液体流量变化的周期性的波。在将入口探头向填料内部移动10mm的实验曲线上则看不到这一现象,这说明10mm左右的填料层将这一波动完全吸收。
2.3.2 液量与液体平均停留时间
实测表明,平均停留时间随液量(即液体流量)的增加而下降(图2-32)。这不难理解,当流量增加时,填料表面的液膜变厚。而从液膜内的流速分布看,必然是远离填料表面的液体流速快。大流量比小流量多出的流量是远离填料表面的部分,因此,平均停留时间下降。并由此引出一个推论:平均停留时间或者说填料层中的平均流速取决于流量和转速,而与液体喷口速度关系不大。实验中,液体流量自1.0m3/h增加到2.5m3/h,喷口速度后者是前者的2.5倍,而平均停留时间仅下降25%。这说明液体进入填料层并与其撞击后,其动能迅速被填料吸收,再向前运动的能量由填料提供,初速度带来的动能已不复存在。(以旋转转子为参照系,转子本身动能为零)。

图2-32 液量与液体平均停留时间(泡沫金属填料,无气)
2.3.3 气量与液体平均停留时间
由图2-33可见,在150m3/h的气量气体作用下,液体的平均停留时间并无显著变化。进一步的结果表明,当气量在0~250m3/h范围内递增变化时,液体的平均停留时间仅稍有下降,这一现象与Keyvani[14]的结果相同。对这一现象,可做如下解释:当转速为600r/min时,液体在床层内径处受到大约50倍于地球引力场的离心力场的作用,此时,气液两相的Δρg同样为地球引力场下的50倍。若要阻止液体的流动,所需的力是相当可观的。当最大气量为250m3/h时,内径处19m/s的气体流速在气液界面上造成的剪应力不足以产生明显影响。也正是由于这一原因,在旋转填充床中泛点气速大大提高。

图2-33 气量对液体平均停留时间的影响
2.3.4 转速与液体平均停留时间
由图2-34可见,对各个流量条件,平均停留时间都随转速的增加而下降;在低转速下,平均停留时间随转速下降的幅度较大,当转速超过800~1000r/min后,平均停留时间保持基本不变。值得注意的是,一些有关旋转填充床传质实验的研究中,也有当转速超过1000r/min后,平均体积传质系数kla基本保持不变的结果。

图2-34 转速对液体平均停留时间的影响(泡沫金属填料,无气)
转速增加,液体在填料表面获得更大的离心加速度。离心加速度的增加会带来流速的增加,则平均停留时间下降。与此同时,在流量不变的前提下,平均停留时间的下降在一定程度上意味着填料表面的液膜厚度下降。液膜内的剪应力τ=-μdu/dy随液膜内速度梯度du/dy值的增加而增加。如果在一定范围内,流速随转速的增加而增加,液膜厚度随转速的增加而减小,则du/dy变化就会更大,液膜内部的剪应力将随转速迅速增加,这对液膜的变薄和流速的增加都起着阻滞作用,使得二者的变化趋势变缓。
2.3.5 方差
有关方差的计算,可依照方差的加成性进行。


用对比时间表示的方差代表了填料中液体的返混程度。当停留时间很短时,进出口之间方差与平均停留时间在测量上的微小误差都会对Δσ2值产生较大影响。尽管如此,也可以从总的统计数据看出旋转填充床的液体流动特性。在郭锴的实验中,对于没有气相流动的实验点,总平均的Δσ2值约为0.5。借用化学反应工程中的多级串联槽模型来判断液体在填料中的返混程度。模型参数n=1/Δσ2,以总平均的Δσ2值0.5代入得n=2,即液体在旋转填充床中的返混程度相当于二级串联的理想混合釜,其E(θ)曲线如图2-35所示。

图2-35 多级串联釜模型二级理想混合停留时间分布曲线
值得注意的是,将入口探头沿半径方向向外移动10mm的数据的平均方差为0.17,仅为全程方差值的1/3,此时,平均停留时间与全程数据没有明显差别。产生这一方差的填料是全部填料的93%,换言之,在内缘处7%的填料造成了全部混合的70%。就混合强度而言,内缘处10mm内的混合强度数倍于填料的其他部位。因此,内缘处液体混合的剧烈程度是不言而喻的。
这就给了我们一个重要的启示:在填料内缘处,液体在极短的时间内(几十毫秒数量级)就得到了充分的混合,其混合程度之好是其他混合设备难以做到的。旋转填充床的这一特性为它的应用(如超重力反应沉淀法制备纳米材料)开拓了新的领域。
分析填料内缘产生剧烈混合的原因,一是有填料与来流液体的碰撞,二是已经附着在填料表面的液体与飞行中的来流的碰撞。与此形成对照的是,在填料主体部分,液体的返混较小,偏向于平推流。从实验观察的结果来看,填料入口处与填料主体部分的区别在于入口处存在填料与来流在周向上的碰撞。因此,有理由得出这一推论,剧烈的混合是由于填料(包括附着在填料上的液体)与其周向速度有较大不同的液体的碰撞所致。在填料主体部分,由于液体与填料的周向速度基本相同,不存在剧烈的混合,与填料内缘相比,在混合的机制上有较大的差别。
2.3.6 停留时间与持液量
Basic和Dudukovic[10,11]等通过测量电导的方法,进行过旋转填充床中持液量的研究,但由于所用的填料孔隙率只有30%左右,其结果与高孔隙率填料有很大不同。我们可通过测量停留时间的方法进行比较研究,持液量定义为单位体积的床层所持液体体积。

由前面所得平均停留时间,可直接计算出转子填料的持液量。

由式(2-49)可以看出,持液量是液体流量与平均停留时间的乘积,填料所表现出的持液量与液体流量的关系实质上是停留时间与液体流量的关系。它反映了在流量变化引起停留时间变化的幅度,因此,持液量这一参数并非独立变量。当然,持液量可以反映出床层的一些特性,但从更深层次而言,需要认真研究的是停留时间而不是持液量。如图2-36显示,持液量随液量增加而增加,随转速的升高而下降。

图2-36 液量与持液量关系