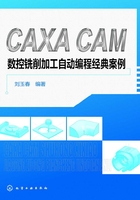
[实例1-3] 凸轮零件的实体造型与加工
按照图1-60所示的尺寸生成凸轮零件加工实体造型。并生成凸轮内孔、凸轮零件内孔区域加工程序、凸轮零件上曲面精加工程序。

图1-60 凸轮零件图及基圆展开图
一、凸轮零件实体造型
① 在曲线选项卡中,单击曲线生成栏中的“圆”按钮 在曲线选项卡中,单击曲线生成栏中的“圆”按钮,在立即菜单中选择“圆心 半径”方式, 做出R85mm、R100mm、R115mm的圆。如图1-61所示。
② 在“特征管理”里选择“平面XY”为基准面,单击状态控制栏中的“草图绘制”按钮(或按F2键),进入草图绘制状态。单击曲线生成栏中的“投影曲线”按钮
,拾取R85mm、R115mm的圆线,完成草图绘制,如图1-62所示。

图1-61 绘制圆

图1-62 绘制草图圆
③ 再次单击曲线选项卡中的“草图绘制”按钮 再次单击曲线选项卡中的“草图绘制”按钮,退出草图绘制。
④ 在特征选项卡中,单击特征生成栏的“拉伸增料”按钮 在特征选项卡中,单击特征生成栏的“拉伸增料”按钮,弹出“拉伸增料”对话框,并填写拉伸增料的相关参数(如拉伸类型、拉伸深度等),填写结果如图1-63所示。在选择拉伸对象时,移动光标至所绘制草图0,单击左键拾取后,单击“确定”按钮,完成拉伸增料,如图1-64所示。

图1-63 拉伸增料对话框

图1-64 圆柱体造型
⑤ 在曲线选项卡中,单击曲线生成栏中的“点”按钮 在曲线选项卡中,单击曲线生成栏中的“点”按钮,在立即菜单中选择“批量点”“等分点”方式,输入等分段数8,回车后,拾取R85mm、R100mm的圆线,完成圆周等分。如图1-65所示。
⑥ 按F9键,切换到YOZ平面。在曲线选项卡中,单击曲线生成栏中的“直线”图标,在立即菜单中选择“两点线”“连续”“正交”“长度”方式,输入长度20,回车后,捕捉等分点,绘制长度为20mm的直线。同样方法,在其它等分点按照图1-60凸轮零件图及基圆展开图所给的尺寸绘制不同长度的直线,如图1-66所示。

图1-65 等分圆周

图1-66 绘制直线
⑦ 在曲线选项卡中,单击曲线生成栏中的“样条”图标 在曲线选项卡中,单击曲线生成栏中的“样条”图标,在立即菜单中选择缺省切矢、开曲线。依次拾取多个直线上面的端点,按右键确认,样条曲线生成。如图1-67所示。
⑧ 在曲面选项卡中,单击曲面生成栏中的“直纹面”图标 在曲面选项卡中,单击曲面生成栏中的“直纹面”图标,在立即菜单中选择直纹面生成“曲线+曲线”方式。然后拾取第一条样条曲线,拾取第二条样条曲线,拾取完毕立即生成直纹面。如图1-68所示。
⑨ 单击圆柱实体上平表面,单击状态控制栏中的“草图绘制”按钮 (或按F2键),进入草图绘制状态。单击曲线生成栏中的“投影曲线”按钮
,拾取R85mm、R100mm的圆线,完成草图绘制,单击曲线选项卡中的“草图绘制”按钮
的圆线,完成草图绘制,单击曲线选项卡中的“草图绘制”按钮,退出草图绘制。

图1-67 绘制样条曲线

图1-68 绘制空间曲面
⑩ 在特征选项卡中,单击特征生成栏的“拉伸增料”按钮 在特征选项卡中,单击特征生成栏的“拉伸增料”按钮,弹出“拉伸增料”对话框,并填写拉伸增料的相关参数,拉伸深度25。在选择拉伸对象时,移动光标至所绘制草图1,单击左键拾取后,单击“确定”按钮,完成拉伸增料,如图1-69所示。

图1-69 拉伸实体

图1-70 延伸曲面
在曲面选项卡中,单击曲面编辑生成栏中的“曲面延伸”图标,在立即菜单中选择“长度延伸”方式,输入长度值5。单击曲面两边,延伸完成。如图1-70所示。
在特征选项卡中,单击除料生成栏中的“裁剪”图标,弹出“曲面裁剪除料”对话框,如图 1-71所示。拾取曲面,确定除料方向选择,单击“确定”完成操作。如图1-72所示。

图1-71 曲面剪裁除料对话框

图1-72 曲面剪裁实体
二、凸轮零件加工与仿真
由零件图可知该工件加工部位为凸轮零件外平台加工、凸轮零件内孔区域加工
和凸轮零件曲面粗精加工。各加工工步刀具直径见表1-1。
表1-1 刀具表

双击特征树中的“毛坯”,弹出毛坯定义对话框。类型选择圆柱形,然后单击参照模型。单击“确定”按钮,毛坯定义完成。
1.凸轮零件外平台加工
① 在加工选项卡中,单击二轴加工工具栏中的“平面区域粗加工”按钮在加工选项卡中,单击二轴加工工具栏中的“平面区域粗加工”按钮,弹出“平面区域粗加工(编辑)”对话框,如图1-73所示。设置相关加工参数,环切加工,选择从外向里方式。顶层高度40,底层高度15,行距为1。

图1-73 平面区域粗加工(编辑)对话框
② 其他各项参数设置完成后,单击“确定”按钮退出“平面区域粗加工(编辑)”对话框,系统进行刀路运算,加工轨迹如图1-74所示。
③ 在加工选项卡中,单击仿真工具栏中的“线框仿真”按钮,单击左键拾取平面区域粗加工轨迹,单击右键拾取结束,开始线框仿真,如图1-75所示。

图1-74 凸轮零件外平台加工轨迹

图1-75 外平台加工轨迹仿真
2.凸轮零件内孔区域加工
① 在加工选项卡中,单击二轴加工工具栏中的“平面区域粗加工”按钮在加工选项卡中,单击二轴加工工具栏中的“平面区域粗加工”按钮,弹出“平面区域粗加工(编辑)”对话框,如图1-76所示。设置相关加工参数,环切加工,选择从里向外方式。顶层高度40,底层高度0,行距为1。

图1-76 平面区域粗加工(编辑)对话框
② 其他各项参数设置完成后,单击“确定”按钮退出“平面区域粗加工(编辑)”对话框,系统进行刀路运算,加工轨迹如图1-77所示。
③ 在加工选项卡中,单击仿真工具栏中的“线框仿真”按钮,单击左键拾取平面区域粗加工轨迹,单击右键拾取结束,开始线框仿真,如图1-78所示。

图1-77 凸轮零件内孔区域轨迹

图1-78 内孔区域轨迹仿真
3. 凸轮零件曲面精加工
① 在加工选项卡中,单击二轴加工工具栏中的“曲面区域精加工”按钮在加工选项卡中,单击二轴加工工具栏中的“曲面区域精加工”按钮,弹出“曲面区域精加工(编辑)”对话框,如图1-79所示。此加工功能是生成加工曲面上的封闭区域的刀具轨迹,适合3轴加工。设置相关加工参数,环切加工,选择从里向外方式。行距为4。
② 加工参数设置完成后,单击“确定”按钮退出“曲面区域精加工(编辑)”对话框,系统进行刀路运算,生成加工轨迹如图1-80所示。
③ 在加工选项卡中,单击仿真工具栏中的“线框仿真”按钮,单击左键拾取曲面区域精加工轨迹,单击右键拾取结束,开始线框仿真,如图1-81所示。

图1-79 曲面区域精加工(编辑)对话框

图1-80 凸轮零件曲面精加工轨迹

图1-81 曲面精加工轨迹仿真
④ 在加工选项卡中,单击后置处理工具栏中的“后置处理”按钮,弹出“生成后置代码”对话框,如图1-82所示。更改要生成的文件名,选择fanuc数控系统,单击“确定”后拾取加工轨迹,最终生成参数线精加工G代码。如图1-83所示。其他加工轨迹G代码生成方法一样,就不一一叙述了。

图1-82 生成后置代码对话框

图1-83 凸轮零件曲面精加工G代码