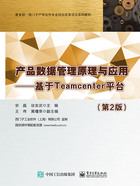
1.1.1 PDM产生的背景
从20世纪的六七十年代开始,企业在设计和生产过程中逐渐开始应用CAD、CAM等软件与技术。一方面,这些软件和技术的使用极大地促进了企业生产力的发展,有效地提高了产品设计和制造的效率,但各软件应用单元自成体系,彼此之间缺少有效的信息共享和利用,形成所谓的“信息孤岛”,阻碍了企业设计生产效率的进一步提高。
另一方面,随着CAD/CAPP/CAM/CAE等软件的广泛应用,计算机产生的各种数据资料迅速增加。在产品全生命周期过程中,从市场分析、产品设计到制造、装配、销售、售后服务等环节都会产生大量相关数据,如市场分析报告、设计信息、加工图纸、零件加工工艺、数控加工程序清单、仿真测试结果分析,以及各种说明书等,其数据量往往是海量的。由此引发一系列产品数据管理问题:不同部门产品信息如何查询、传递等以实现信息共享;如何保证技术中心和各部门图纸版本的一致性;如何保证各部门的数据不会流失泄密;如何简化系列产品开发,保证各部门 BOM 的准确性;如何跟踪工作状态并记录备案;如何分析更改影响并及时通知各部门等。如何消除“信息孤岛”,有效地管理海量数据,突破企业信息化瓶颈,是企业面临的一大难题,也是企业在未来竞争中保持领先的关键因素。
PDM正是在这一背景下应运而生的一项管理思想和技术。当今企业面临越来越激烈的市场竞争,市场对企业在 P、T、Q、C、S 五个方面提出了更高的要求,即设计生产市场需要的产品(Product)、缩短产品的上市时间(Time)、保证良好的产品质量(Quality)、降低产品的综合成本(Cost)、提供优质的售后服务(Service)。PDM以提高企业满足市场P、T、Q、C、S五个方面要求的能力为目标,在产品数据与工作流集成思想指导下,继承并发展了工程数据库、电子数据交换、成组技术、并行工程、产品数据交换、企业业务重组等核心思想,以产品数据和过程为中心,科学合理地对企业业务过程、产品数据和过程进行描述和重组,以便规范化管理产品生命周期中的数据和过程,保持产品数据的一致性和可跟踪性。PDM系统的核心思想是数据共享、人员协同、过程优化、减少企业信息化瓶颈。
PDM是当今计算机应用领域的重要技术之一。近几年来,PDM是产品制造工业中发展最快的一种技术。PDM的应用给企业带来了非凡的成就。据国外统计资料,PDM的应用能使产品设计周期缩短25%,减少工程设计修改4%,加快产品投放市场进度50%~80%,总成本削减25%以上。国外的一些汽车、飞机公司实施PDM后均大大提高了企业的效益。国内据对机电工业近500家企业调查显示,新产品开发周期平均长达24个月,其中单件、小批量产品的生产技术准备周期约占供货期的32%,有的高达60%,采用PDM技术后,可缩短生产周期50%~80%。